What is Supply Chain Management?
Supply Chain Management (SCM) is a comprehensive and systematic approach to overseeing the entire process of producing and delivering products or services, from the initial stages of raw material acquisition to the final delivery to the end consumer. Its main goal is to efficiently coordinate and integrate all the activities involved in the production and distribution of goods or services to meet customer demands while optimizing costs and maintaining quality.
Importance
The importance of supply chain management can be emphasized for the following reasons:
- Optimize operational efficiency — By facilitating the seamless flow of goods, information, and services from raw material suppliers to end consumers, SCM helps minimize waste, reduce excess inventory, and streamline production processes, thereby enhancing overall cost efficiency.
- Prioritize customer satisfaction — A well-managed supply chain leads to timely deliveries, accurate order fulfillment, and consistent product availability. Meeting customer expectations on these fosters loyalty, elevates brand reputation, and, ultimately, contributes to sustainable business growth.
- Future-proof business — SCM not only addresses current customer needs but also anticipates future demands through demand forecasting, ensuring that businesses remain agile and responsive in meeting evolving market requirements.
- Drive competitive advantage — Organizations that can deliver products faster, at lower costs, or with greater flexibility gain a distinct edge in the market. This competitive advantage is particularly crucial in industries characterized by rapid changes and intense competition.
- Facilitate risk management — Effective SCM helps businesses navigate unforeseen challenges, such as supply chain disruptions, geopolitical issues, or unexpected shifts in market demand.
What is the Difference Between Logistics and Supply Chain Management?
Logistics or logistics management are often covered when supply chain management is being taken into account. While there may be a few overlaps in their purposes, they differ greatly based on their focus and scope.
Logistics primarily deals with the physical movement, storage, and transportation of goods from one point to another within the supply chain. It encompasses activities such as inventory management, warehousing, transportation, and distribution. Logistics management is more tactical and operational, concentrating on the efficient and cost-effective execution of these specific tasks to ensure products are delivered on time and in the right quantity.
On the other hand, supply chain management encompasses the entire lifecycle of a product, as well as strategic planning, procurement, manufacturing, distribution, and even aspects like demand forecasting and Supplier Relationship Management (SRM). Hence, SCM is concerned with optimizing interconnected activities in the entire supply chain while considering long-term strategic goals.
Components
The following interconnected components of supply chain management must work together to ensure the efficient flow of goods, information, and services throughout the entire supply chain:
- Strategic Planning — involves the development of a comprehensive strategy that aligns supply chain activities with overall business goals
- Procurement — encompasses the process of sourcing and acquiring the necessary raw materials, components, and goods from suppliers
- Manufacturing or Production — focuses on transforming raw materials into finished goods through various production processes
- Distribution — involves the logistics of getting finished products from the manufacturing facility to distribution centers and, ultimately, to retailers or end consumers
- Transportation — addresses the movement of goods between different points in the supply chain
- Warehousing — entails the storage and management of inventory at various points in the supply chain
- Inventory Management — focuses on optimizing the levels of inventory to meet demand while minimizing holding costs
- Demand Forecasting — involves predicting future customer demand based on historical data, market trends, and other relevant factors
- Supplier Relationship Management — encompasses the management of relationships with suppliers
- Information Technology (IT) Systems — covers the use of technology to facilitate communication, data exchange, and coordination within the supply chain
- Risk Management — involves identifying and mitigating potential risks that could disrupt the supply chain
- Performance Measurement and Analytics — encompasses the use of Key Performance Indicators (KPIs) and analytics to assess and improve the efficiency and effectiveness of supply chain processes
What are the 5 Basic Steps of Supply Chain Management?
Generally, organizations can follow a structure in implementing effective strategies for managing the entire supply chain. This way, a holistic approach can be applied every step of the way.
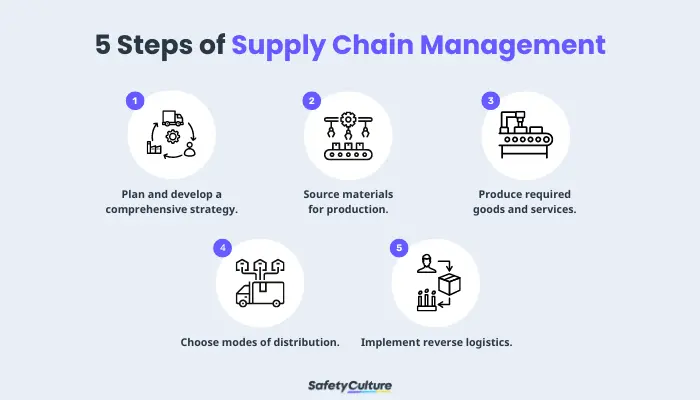
5 Steps of Supply Chain Management
Here are the five key steps of the supply chain management process:
1. Plan and develop a comprehensive strategy for the overall supply chain activities.
Strategic planning in SCM involves the development of a comprehensive strategy that aligns supply chain activities with overall business goals. This includes decisions related to sourcing, manufacturing, distribution, and customer service.
Organizations need to assess market demands, consider competitive factors, and define the role of the supply chain in achieving long-term objectives. These lay the foundation for the entire supply chain, guiding subsequent decisions and actions.
2. Source materials for production.
Procurement is the process of sourcing and acquiring raw materials, components, and goods from suppliers. This step involves selecting reliable suppliers, negotiating contracts, and managing relationships to ensure a stable and cost-effective supply of materials.
3. Produce required goods and services.
Manufacturing or production focuses on transforming raw materials into finished goods through various production processes. This step also includes decisions about production methods, technology utilization, and capacity planning to ensure that products are produced in the right quantity and at the right time.
4. Choose modes of distribution.
Distribution involves the logistics of getting finished products from the manufacturing facility to distribution centers and, ultimately, to retailers or end consumers. This step includes decisions related to transportation, storage, and order fulfillment. Ultimately, the aim is to optimize the movement of goods, reduce lead times, and meet customer expectations for timely delivery.
5. Implement reverse logistics.
Typically included under the umbrella of reverse logistics, post-delivery customer support that deals with returned goods helps businesses maintain good customer relationships. On the other hand, retailers, manufacturers, or any other customer-facing entity in the supply chain returns defective, low-quality, or excessive materials or products to suppliers. This helps minimize waste and even recycle qualified goods.
Create Your Own Supply Chain Management Checklist
Eliminate manual tasks and streamline your operations.
Get started for FREEExamples
The following supply chain management examples show how each SCM phase can be applied in certain industries:
Manufacturing Industry — Automobile Production
- Strategic Planning — An automobile manufacturer aims to optimize its supply chain. The company then assesses suppliers for key components like engines, tires, and electronics to ensure a balance between cost-effectiveness and quality. Apart from that, aligning production with market demand is also part of the overall strategy.
- Procurement — The manufacturer establishes contracts with selected suppliers, negotiating bulk purchase agreements to secure favorable pricing.
- Manufacturing or Production — The automobile manufacturer implements streamlined production lines and just-in-time manufacturing practices to help minimize inventory holding costs while ensuring efficient production and assembly.
- Distribution — Finished automobiles are then transported to regional distribution centers to optimize transportation routes, reduce lead times, and ensure a well-coordinated supply chain. The company also utilizes a combination of dedicated transport fleets and third-party logistics providers for transportation.
- Reverse Logistics — The manufacturer develops processes to handle returned parts, salvage usable components, and responsibly manage the disposal of automotive waste.
Retail Industry — Clothing Retailer
- Strategic Planning — A clothing retailer aims to improve its supply chain to meet changing fashion trends. For this, they strategize demand forecasting measures on different styles and sizes. The retailer also collaborates with fashion designers and suppliers to align production with anticipated customer preferences.
- Procurement — The retailer establishes relationships with textile manufacturers and clothing suppliers for their procurement efforts, focusing on securing a variety of clothing styles in line with market trends while negotiating favorable terms for bulk purchases.
- Manufacturing or Production — While not directly involved in manufacturing, the retailer works closely with suppliers to customize clothing orders and ensure timely production. Such collaborative relationships help them make quick adjustments to production based on changing fashion demands.
- Distribution — Clothing items are distributed to regional warehouses and individual stores to prioritize quick replenishment, efficient inventory turnover, and restock popular items rapidly. The retailer also uses a mix of transportation modes, including shipping and trucking, to distribute clothing items.
- Reverse Logistics — The retailer implements processes to efficiently handle returned clothing, endorse reusable materials for recycling or repurposing, and dispose of unsold inventory while adhering to responsible practices.
Sustainable SCM Practices
Embedding a mindset and culture of sustainability is essential for businesses looking to reduce their environmental impact, enhance social responsibility, and achieve long-term resilience, especially when considering their SCM efforts.
To guide organizations, here are key sustainable practices in SCM to implement:
- Prioritize green procurement by sourcing materials from environmentally responsible suppliers.
- Optimize transportation for energy efficiency by utilizing fuel-efficient vehicles and exploring alternative energy sources.
- Embrace circular economy principles by designing recyclable products and incorporating recycled materials.
- Promote supplier diversity and social responsibility by working with businesses adhering to fair labor practices.
- Minimize packaging waste through eco-friendly materials and optimized packaging design.
- Implement lean inventory management to reduce excess stocks and improve operational efficiency.
- Monitor and reduce the carbon footprint of the supply chain through tracking emissions and offsetting initiatives.
- Integrate technology, such as Internet of Things (IoT) sensors and data analytics, to enhance supply chain visibility.
- Foster collaboration and transparency with stakeholders to promote sustainable practices.
- Conduct life cycle assessments to evaluate the environmental impact of products.
- Cultivate a continuous improvement culture by encouraging employees to contribute to sustainability efforts.
- Utilize scalable and easy-to-integrate solutions and tools to implement a holistic way of monitoring and optimizing supply chain operations.
Scale Your Enterprise Operations with Customizable Solutions
✓ Scale ✓ Data ✓ Security ✓ Integration ✓ Teams
Learn MoreRegulatory Considerations
Managing an organization’s supply chain doesn’t stop at ensuring every step or phase is well-optimized and resource-efficient. It also involves adhering to various standards and regulations.
Compliance plays a big part in ensuring the legality, safety, and efficiency of supply chain operations. Here are three key regulatory considerations that organizations must maintain lawful supply chain practices:
- Industry-Specific Regulations — Different industries often have specific regulations governing supply chain practices. For example, pharmaceutical companies may be subject to stringent regulations regarding the transportation and storage of medications, while the food industry must comply with laws related to safety and labeling.
- Global Trade Regulations — International supply chains are subject to customs regulations, import/export restrictions, and trade agreements between countries. Navigating such requires a comprehensive understanding of the legal requirements in each jurisdiction to avoid legal issues, tariffs, and disruptions to cross-border operations.
- ISO Standards — The International Organization for Standardization (ISO) develops and publishes standards that provide guidelines for various aspects of supply chain management. Adhering to ISO standards, including ISO 9001 for quality management and ISO 14001 for environmental management, not only ensures regulatory compliance but also demonstrates a commitment to quality and environmental responsibility in supply chain operations.
FAQs About Supply Chain Management
Since supply chain management entails complex phases to ensure a holistic strategy, companies inevitably encounter challenges along the way. Some notable ones include the following:
- Uncertainty and Disruptions
- Complexity and Globalization
- Inventory Management
- Technological Integration
- Supplier Relationships
Technological solutions such as automated systems and data analytics enable real-time inventory tracking, reducing lead times and improving demand forecasting accuracy. Radio-Frequency Identification (RFID) and IoT can also be used to improve asset visibility, ensuring better control over the movement of goods.
Likewise, cloud-based platforms facilitate seamless collaboration and information sharing among supply chain partners. Lastly, Artificial Intelligence (AI) and machine learning algorithms optimize decision-making processes, contributing to overall supply chain agility and responsiveness.
Globalization impacts supply chain management by expanding networks and increasing complexity. Since companies that source materials and components from diverse international suppliers can face amplified effects of disruptions (e.g., natural disasters or geopolitical events), careful coordination and risk management are required.
Cultural differences, varying regulations, and logistics challenges also pose additional hurdles in global supply chain operations. However, globalization offers opportunities for cost reduction, market expansion, and access to a broader pool of suppliers and customers.
Reverse logistics involves handling product returns, refurbishing or recycling items, and managing excess or obsolete inventory. Its effective implementation helps minimize waste, recover value from returned goods, and enhance customer satisfaction.
Ultimately, integrating reverse logistics into supply chain management contributes to sustainability, cost efficiency, and customer loyalty.