Qu’est-ce que le Jidoka ?
Jidoka est un principe mis en œuvre dans les processus industriels, selon lequel les machines s’arrêtent automatiquement de fonctionner lorsqu’elles détectent une condition anormale ou un défaut. Les opérateurs tentent de réparer le défaut pour éviter que le problème ne se reproduise. Le jargon lean est d’origine japonaise et se traduit par “autonomation”, une combinaison des mots “autonomous” et “automation”. Littéralement, Jidoka signifie “automatisation avec une touche humaine”, un pilier essentiel du système de production Toyota (TPS) qui a ensuite inspiré la Maison du Lean Manufacturing. Le concept d’intégration de l’intelligence aux machines permet à un seul opérateur de faire fonctionner plusieurs machines avec un minimum d’efforts et aux entreprises de devenir plus rentables grâce à l’augmentation de la productivité.
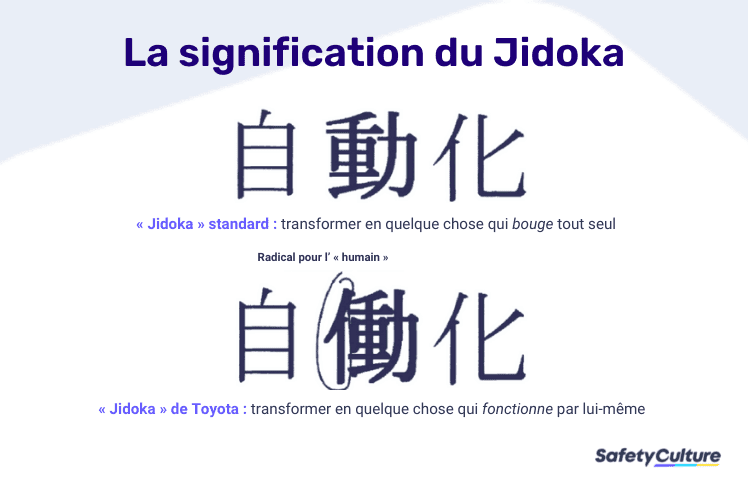
Un mot créé par Toyota, Jidoka signifie inclure l’élément humain dans l’automatisation. | Source d’image
La signification de Jidoka : Histoire et développement
Jidoka est un terme technique créé par Toyota qui se prononce exactement comme le mot japonais pour “automatisation”. automatisation (Jidōka), mais il est écrit différemment. Parce que le caractère pour “être humain” a été ajouté à l’orthographe standard, sa signification a changé. Par conséquent, la définition de Jidoka peut être mieux comprise comme “autonomation”, c’est-à-dire l’automatisation avec une touche humaine, ou l’automatisation autonome.
L’origine du Jidoka remonte à Sakichi Toyoda, le fondateur de Toyota, qui était au départ une entreprise de fabrication de textiles. En 1896, il a mis au point un mécanisme capable de détecter les fils cassés dans un métier à tisser et d’empêcher automatiquement la machine de produire des matériaux défectueux. Avant son invention, les métiers à tisser continuaient à produire des tissus défectueux lorsqu’un fil se cassait, si bien que les ouvriers devaient constamment garder un œil sur chaque machine.
En tant qu’application pratique du principe de Jidoka, le dispositif d’arrêt automatique de la casse de la trame incorporé dans les métiers à tisser montre l’automatisation avec l’intelligence humaine. Il donne à l’équipement la capacité de reconnaître les bonnes pièces des mauvaises de manière autonome, ou sans être surveillé de près par les employés. De ce fait, un seul opérateur peut s’occuper de plusieurs machines, ce qui entraîne des gains de productivité considérables. Non seulement les personnes peuvent être libérées de l’attachement aux machines, mais elles peuvent également être positionnées pour effectuer un travail à plus forte valeur ajoutée dans les opérations commerciales quotidiennes.
Au fil du temps, la signification de Jidoka a évolué, passant du simple arrêt automatique des processus en cas d’irrégularités à la manipulation de plusieurs machines semi-automatisées. Michel Baudin dans son livre Travailler avec des machines : les rouages des opérations Lean avec Jidoka élargit même la liste des définitions généralement admises en y ajoutant l'”automatisation partielle”, c’est-à-dire l’automatisation de tâches dangereuses, pénibles et chronophages qui entraînent une fatigue tout au long d’un poste de travail ou des lésions dues au stress répétitif au cours des mois ou des années.
Cependant, Jidoka à Toyota signifie qu’une machine doit s’arrêter en toute sécurité dès qu’une anomalie se produit. L’objectif n’est pas de faire fonctionner les machines en permanence, mais de les arrêter automatiquement lorsqu’un problème survient. Cette fonction permet d’empêcher que les défauts ne se reproduisent, de prévenir les blessures évitables, de minimiser les dommages matériels et de donner aux équipes les moyens d’adopter des solutions à long terme après examen de la question.
Pourquoi le Jidoka est-il important ?
Le Jidoka est important parce qu’il est l’un des deux piliers fondamentaux du système de production le plus largement adopté dans le monde. Sans elle, la Maison du Lean Manufacturing n’existerait plus. La mise en œuvre de ce principe permet aux entreprises de garantir le développement de produits de haute qualité, car les produits défectueux sont automatiquement détectés tout au long de la procédure. Jidoka dote également les travailleurs de première ligne d’un état d’esprit qui considère chaque problème qu’ils identifient comme une opportunité d’amélioration. Elle entretient une culture d’amélioration continue en tirant des enseignements des défauts de production et en appliquant des solutions instantanément au lieu de les gaspiller par l’inactivité.
Principe Jidoka : 4 éléments du Lean Manufacturing
Il y a 4 éléments de base du principe Jidoka dans l’industrie : détection, arrêt, réponse et prévention. Une bonne maîtrise de ces éléments fondamentaux permet de mieux comprendre le principe et la manière dont il peut être appliqué dans les pratiques commerciales des fabricants :
- Détecter les anomalies : Chaque pièce d’équipement devrait être installée avec la capacité de repérer les erreurs. En outre, un système d’alerte doit être mis en place pour signaler la découverte de toute anomalie telle que des défauts de produits, des erreurs de matières premières et des pannes de machines.
- Arrêt de la production : En cas de détection d’une anomalie, les machines doivent pouvoir cesser automatiquement de fonctionner afin de contenir le problème. Les opérateurs doivent également avoir les moyens d’arrêter manuellement la production au cas où ils remarqueraient quelque chose de non conforme.
- Prendre des mesures : Avec les mécanismes d’arrêt automatique qui interrompent la production, les opérateurs doivent évaluer la situation et demander de l’aide si nécessaire. Les actions correctives doivent être effectuées dans un délai donné pour décider de la reprise ou non de la production.
- Prévenir les récidives : Lorsque des solutions rapides permettent de poursuivre la production, les responsables doivent examiner rétrospectivement le problème afin d’appliquer des solutions permanentes. Lorsque le temps imparti est écoulé et que le problème persiste, une équipe désignée doit mener une enquête pour traiter la cause profonde et poursuivre la production dès que possible.
Comment le Jidoka est-il mis en œuvre ?
Le Jidoka exige un changement de paradigme à l’échelle de l’entreprise, qui ne doit plus négliger des problèmes apparemment mineurs pour respecter les délais, mais prendre la responsabilité de garantir la qualité à la source. Quelle que soit la position d’une organisation dans ce spectre, une chose reste certaine : l’humain est au cœur de Jidoka. La clé d’une mise en œuvre réussie réside dans la collaboration entre les personnes et les machines. En général, il y a 3 étapes simples pour démarrer la performance Jidoka dans la production :
1. Démontrer l’engagement de la direction
Pour que les fabricants soient en mesure de gérer avec succès un système de production, les responsables doivent accorder à la Jidoka le même niveau d’importance qu’au juste-à-temps (JAT). Elles passent souvent à côté d’opportunités de croissance parce qu’elles accordent trop d’importance au flux continu de main-d’œuvre et de matériaux. Cependant, lorsque la direction s’engage à actualiser le Jidoka dans le contexte de l’organisation, une définition claire doit être élaborée et communiquée. Puisqu’il s’agit avant tout d’un principe, tout le monde dans l’entreprise doit être sur la même longueur d’onde quant à sa signification exacte, en commençant par le sommet et en poursuivant par la base.
2. Effectuer des évaluations de l’état de préparation
Avec la direction, transformer le mode de fonctionnement de l’entreprise, utilisez une liste de contrôle Jidoka pour déterminer les besoins spécifiques de mise en œuvre. En procédant à des évaluations de l’état de préparation avec les parties prenantes concernées, l’organisation peut mieux comprendre sa situation et se préparer à des changements tels que l’adaptation à un cadre radicalement nouveau, la documentation détaillée des exigences et la mise en place des éléments clés du système d’amélioration des performances Jidoka, notamment les processus d’évaluation, d’apprentissage organisationnel et d’innovation, entre autres.
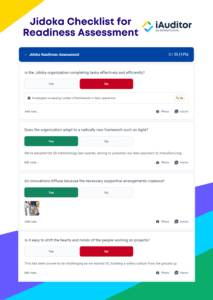
Comment mettre en œuvre Jidoka : Évaluation de l’état de préparation | Voir la liste de contrôle
3. Exécuter des applications pratiques
Après avoir identifié et comblé les lacunes de la mise en œuvre, planifier et lancer un projet Jidoka spécifique avec une équipe interfonctionnelle. L’une des façons les plus rapides de le faire évoluer est de le faire par le biais de Andon le réglage de machines ou de chaînes de montage avec la capacité de déceler les problèmes et d’arrêter la production. En tant que système de gestion visuelle, les opérateurs peuvent efficacement alerter les gestionnaires sur les problèmes afin que les corrections puissent être apportées dès le début. Auparavant, l’opérateur redémarrait normalement la machine lorsqu’elle s’arrêtait à cause d’une erreur. Grâce à une application pratique du Jidoka, les membres du personnel peuvent désormais soulever des problèmes de sécurité ou de qualité et mettre en place des contre-mesures susceptibles d’empêcher la récurrence.
Exemples de Jidoka
L’un des exemples les plus célèbres de Jidoka est le métier à tisser automatique Toyoda de type G, la version perfectionnée du métier de 1896 qui a finalement été brevetée 28 ans plus tard. Non seulement le métier à tisser de 1924 possède des dispositifs d’arrêt automatique, mais il est également doté d’un système de changement de navette, ce qui permet de fournir automatiquement des matériaux à la machine sans réduire la vitesse pendant le fonctionnement en cours.
Un autre exemple de Jidoka est la fonction d’arrêt automatique des machines d’impression modernes lorsque les papiers se coincent. Les imprimantes peuvent détecter si quelque chose d’étrange se produit au niveau de leur alimentation en papier, interrompre le processus d’impression et informer l’utilisateur de l’erreur. Une fois le bourrage papier éliminé, l’impression reprend tout en évitant de détériorer sa qualité et l’imprimante elle-même.
Maintenir le Jidoka avec la technologie d’aujourd’hui
Si le concept de Jidoka existe depuis plus d’un siècle, sa manifestation s’est multipliée avec la quatrième révolution industrielle, ou industrie 4.0. Il ne fait aucun doute qu’il existe une tendance croissante à l’automatisation des opérations industrielles grâce aux technologies de production intelligente. SafetyCulture (anciennement iAuditor) est une plateforme de gestion des opérations qui peut aider les équipes à répondre plus rapidement aux problèmes et à mieux travailler ensemble. Voici comment SafetyCulture (iAuditor) peut aider les organisations à respecter le principe de Jidoka :
Signaler, gérer et documenter les problèmes plus efficacement
Faites passer les rapports sur les problèmes au niveau supérieur grâce à la fonctionnalité SafetyCulture (iAuditor) Observations. Avec l’application mobile, saisissez les informations clés dès que la production s’arrête, afin que votre équipe puisse traiter les problèmes de sécurité ou de qualité avant qu’ils ne deviennent incontrôlables. Grâce à l’application Web, gérez efficacement les problèmes signalés et les enquêtes en cours en accédant à leur statut et à leurs mises à jour depuis un tableau de bord convivial. Les gestionnaires peuvent s’assurer que tous les problèmes identifiés par les applications Jidoka sont correctement documentés et comptabilisés.
Assigner, surveiller et conserver des traces des actions de manière plus efficace
Instaurez une culture du travail d’équipe, de la communication et de la collaboration grâce à la fonction Actions de SafetyCulture (iAuditor) . Affichées dans une chronologie qui ressemble à une conversation, les équipes peuvent discuter et ajouter des photos aux actions correctives ou aux correctifs appliqués et aux solutions mises en œuvre avec des niveaux de priorité et des dates d’échéance. En vous connectant à SafetyCulture (iAuditor) sur des ordinateurs de bureau ou des ordinateurs portables, vous pouvez visualiser toutes les actions assignées dans des graphiques faciles à comprendre pour vous aider à suivre les domaines d’amélioration et à conserver les enregistrements de conformité.
Ajoutez jusqu’à 10 membres d’équipe avec un compte SafetyCulture (iAuditor) gratuit aujourd’hui !