Qu’est-ce que le Value Stream Mapping (VSM) ?
La cartographie de la chaîne de valeur ou Value Stream Mapping (VSM) est l’un des principes clés des outils de l’industrie lean. Il s’agit d’avoir une vue d’ensemble du processus de bout en bout (du fournisseur au consommateur) pour aider à analyser et à gérer le flux de matériaux et d’informations, à identifier les gaspillages et à déterminer les étapes ou les éléments qui n’apportent pas de valeur ajoutée pour le client.
La VSM est également connue sous le nom de “cartographie des flux de matières et d’informations”. Il utilise un système de symboles standard pour représenter le flux de marchandises. L’Université de Washington l’a défini comme “les étapes du processus allant de l’entrée de la commande à la livraison”. Une excellente définition simple de la VSM est donnée par Cutter: “La cartographie du flux de valeur (VSM) est une méthode de l’industrie Lean utilisée pour analyser et gérer le flux de matériaux/informations/produits afin de pouvoir apporter un produit à un client. Les éléments sont cartographiés comme “ajoutant de la valeur” ou “n’ajoutant pas de valeur” du point de vue du client, dans le but de découvrir ce qui n’ajoute pas de valeur.”
En termes simples, la VSM est une technique lean permettant de trouver et d’éliminer les gaspillages dans le flux des processus, ce qui contribuera éventuellement aux efforts d’amélioration continue.
6 outils clés de la production lean
Les origines du VSM sont souvent attribuées à Toyota Motor Corporation qui a popularisé le lean manufacturing. Le concept de “lean” se concentre sur l’élimination des “mudas“dans l’industrie pour atteindre son objectif principal de créer plus de valeur pour les clients. Vous trouverez ci-dessous les 6 outils clés utilisés dans l’industrie lean pour éliminer le gaspillage dans les processus :
- Cartographie de la chaîne de valeur (VSM) – un outil de visualisation utilisé pour identifier les déchets dans le processus et la valeur ajoutée par chaque étape du processus.
- 5S Lean – une manière systématique d’organiser les lieux de travail en éliminant le gaspillage à l’aide des 5S : Trier (Seiri), Mettre en ordre (Seiton), Faire briller (Seiso), Standardiser (Seiketsu) et Maintenir (Shitsuke).
- Total Productive Maintenance (TPM) – est une approche de l’entretien proactif et préventif des équipements afin d’éviter les pannes et les défauts.
- Le système SMED (Single-Minute Exchange of Die) – est un système permettant de réduire le temps utilisé pour les changements d’outils.
- Poka-Yoke – est une technique de normalisation du travail utilisée pour corriger les défauts potentiels.
- Kaizen – est une philosophie commerciale japonaise qui signifie “amélioration continue” ou “changement pour le mieux”.
La philosophie qui sous-tend tous les outils Lean consiste à éliminer les déchets de vos processus afin de maximiser les bénéfices. L’accent est également mis sur des détails tels que les personnes qui participent au processus, les processus qui se déroulent et le temps que prend chaque processus.
Objectifs du VSM
L’objectif de la VSM est d’examiner d’un œil critique chaque étape du processus de industrie afin de faire ce qui suit :
#1 Identifier les déchets
Le gaspillage peut être lié au temps, au matériel ou au travail. Mais il peut aussi être lié à l’utilisation de la main-d’œuvre ainsi qu’à une mauvaise planification. L’infographie ci-dessous présente les 8 sources de gaspillage en entreprise.
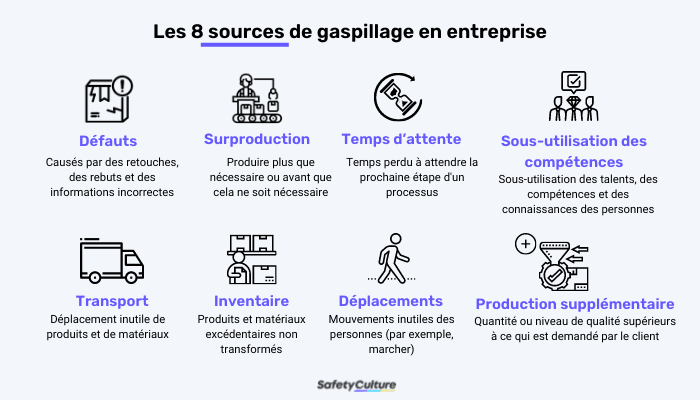
8 sources de gaspillage en entreprise | Source: Visual Paradigm
Après l’identification des déchets, on détermine les types d’opérations ou d’activités qui se produisent au cours du déroulement du processus. Il en existe trois types :
- Opérations sans valeur ajoutée (NVA) – se rapporte à toute action qui n’ajoute pas de valeur à un produit ou à un service.
- Opérations nécessaires mais sans valeur ajoutée (NNVA) – Il s’agit des activités ou des processus qui ne créent pas de valeur pour le client, mais qui sont essentiels à votre entreprise.
- Les opérations à valeur ajoutée (VA) – concerne la valeur donnée par vos clients, car la valeur est toujours déterminée par le client ; c’est ce pour quoi les clients paient.
#2 Réduire les temps de cycle des processus
La VSM fournit une vision claire du processus de travail – le type d’activités concernées. Cela permet également de visualiser la durée du cycle du processus, c’est-à-dire le temps nécessaire pour que les articles passent par un processus. Une fois les déchets identifiés, il y aura automatiquement une réduction de la durée du processus. Il en résulte un processus plus optimisé.
#3 Éliminer les transferts
Handoffs signifie “temps d’attente” ou lorsqu’un travailleur doit attendre un autre pour accomplir une tâche. Ils sont le plus souvent le lieu ou le moment où les choses tournent mal. Le manque de communication peut entraîner des retards et des gaspillages. Le VSM identifie les transferts et aide à déterminer ce qui fonctionne et ce qui pourrait être amélioré.
#4 Mettre en œuvre l’amélioration continue
L’utilisation de la VSM vous permet d’identifier où se trouvent les sources de gaspillage et combien de temps est utilisé dans chaque cycle à chaque étape du processus, ce qui vous donne des possibilités de gagner du temps et de réduire le coût de production. Son objectif est de faire en sorte que les entreprises voient des domaines d’amélioration pour les aider à se développer et à s’étendre avec succès.
Autres outils Lean pour identifier la valeur et le gaspillage
Il existe un certain nombre de techniques pour aider l’entreprise à identifier les activités à forte valeur ajoutée ainsi que les gaspillages.
- 5 pourquoi – se rapporte à la technique qui consiste à trouver la cause profonde de tout problème afin d’identifier les possibilités d’amélioration
- Résolution de problèmes A3 – se rapporte à la technique de l’analyse des causes profondes, qui peut souvent faciliter l’identification des activités à valeur ajoutée et l’élimination des opérations inefficaces.
- Les Gemba Walk– Il s’agit d’une technique qui permet à la direction d’observer la façon dont le travail est effectué et de voir où la valeur est créée.
Étapes de la création d’une carte de la chaîne de valeur
Les Value Stream Mapping peuvent être créées avec des illustrations d’organigramme ou avec des logiciels comme autoCAD en suivant les étapes ci-dessous données par Visual Paradigm :
Étape 1: dessiner lesboîtes de processus qui seront fournies avec les différentes étapes du processus, en partant du côté fournisseur pour aller vers le côté client dans la zone des flux d’information.
Étape n° 2 : Dessiner les boîtes de processus qui seront fournies avec les différents types de étapes de production sous les flux de matériaux section
Étape 3 : Dessin des boîtes de données sous chaque case des étapes de production, dans lesquelles sont saisies les données de chacune des étapes du processus dessinées sur la carte.
Étape 4 : dessinez les méthodes de connexion comme les symboles de flèches de poussée entre les boîtes de processus.
Étape n°5 : établir le lien entre les fournisseurs et les clients. La dernière étape est l’échelle des délais, qui se trouve au bas de la carte. Il montre la durée du cycle du processus dans la chaîne de valeur.
L’illustration ci-dessous montre à quoi ressemble une carte typique de la chaîne de valeur :
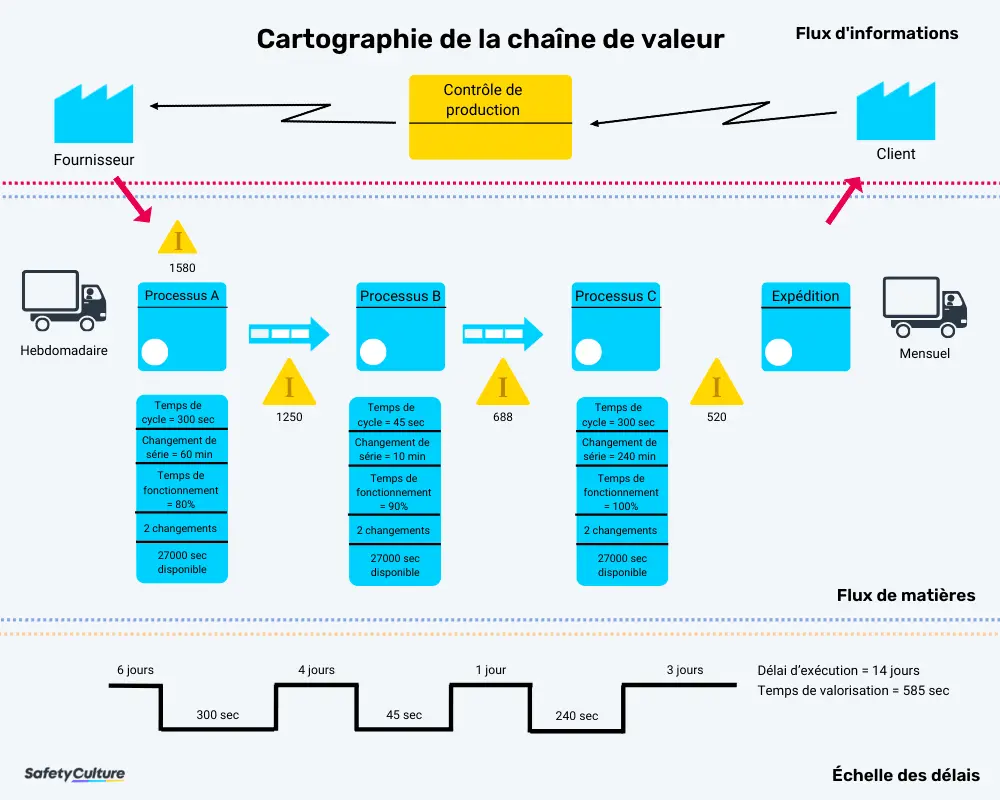
Modèle de Value Stream Mapping | Source : Visual Paradigm
Une carte de la chaîne de valeur vous aide à voir où vous pouvez improviser et utiliser vos ressources inutilisées ou mal utilisées pour produire du bon travail.
- La section supérieure d’un VSM est l’endroit où les informations circulent. Les personnes impliquées dans le flux, par exemple le fournisseur, le fabricant/gestionnaire et le consommateur, sont à l’origine des activités du processus. Par exemple, le client donne les détails de ce qu’il veut et quand il en a besoin. Ensuite, le responsable donne des ordres et des instructions sur la manière de procéder et sur les sources d’approvisionnement. vous disent ce qu’ils veulent, où ils le veulent et quand ils le veulent.
- La section centrale est celle où le matériel circule. Elle comprend tous les processus impliqués dans la fabrication du produit, depuis l’acquisition des matières premières auprès du fournisseur jusqu’à l’achèvement du produit.
- La section inférieure est celle où se trouve le échelle des délais est situé. Il montre tout le temps pris pour chaque cycle ou processus et les écarts entre deux étapes du processus ou les temps d’arrêt. Lorsque le type d’activité est déterminé, qu’il s’agisse de VA, NVA ou NNVA, cela permet d’éliminer les temps d’arrêt.
Voir la liste des symboles ou icônes typiques utilisés dans les cartes de flux de valeur ici : Ingénieur de projet
Types de cartes de la chaîne de valeur
Il existe deux types de cartes de la chaîne de valeur :
(1) Carte de la chaîne de valeur de l’état actuel – Il est créé avant de réaliser le futur VSM par l’analyse et le suivi des flux d’informations et de matières. Cela permet de déterminer à quoi ressemble le processus à l’heure actuelle ; et
(2) Carte de la chaîne de valeur de l’état futur – Cette étape se concentre sur ce à quoi ressemblera la future carte de la chaîne de valeur, y compris les améliorations idéales du processus.
Étapes de la cartographie de la chaîne de valeur
Analyser correctement tous les flux et processus impliqués dans la livraison de produits ou de services au client, cartographie est utilisée.
Voici 7 étapes à suivre pour analyser tout processus de fabrication :
- Documenter le processus actuel – Dressez la liste de toutes les activités en cours.
- Dressez la liste de toutes les étapes du processus – dressez la liste de toutes les étapes, du début jusqu’au stade où la demande du client est satisfaite.
- Identifiez les étapes qui apportent une valeur ajoutée – dressez la liste de toutes les étapes qui apportent une valeur ajoutée au client et de celles qui n’en apportent pas. Ensuite, déterminez ce qui peut se passer si ces étapes sont supprimées du processus.
- Visualisez ce à quoi ressemblera le processus lorsque tous les déchets seront éliminés – vous devez définir ce à quoi il ressemblerait si vous pouviez éradiquer tous les déchets et les activités qui n’apportent pas de valeur ajoutée.
- Identifiez les parties du processus actuel qui entravent la réalisation de votre processus idéal.
- Déterminez les domaines qui peuvent être améliorés et développez les moyens possibles de les améliorer – cela peut signifier une amélioration de l’équipement ou des outils. Cela peut également signifier que vous devez ajouter du personnel ou que vos travailleurs ont besoin d’une formation supplémentaire.
- Attribuer les tâches et mettre en œuvre les plans – cette étape est celle où les tâches sont attribuées aux personnes ou groupes appropriés pour exécuter correctement les plans.
SafetyCulture (iAuditor) pour la cartographie de la chaîne de valeur (Value Stream Mapping)
À l’origine, le VSM a été créé sur papier, ce qui pouvait devenir désordonné, difficile à gérer et à comprendre à mesure que les processus et les données s’accumulaient. L’utilisation d’un logiciel pour numériser vos processus est un moyen plus facile et plus efficace de cartographier vos flux d’affaires. Il sera également plus efficace de les partager dans l’ensemble de l’organisation si vous disposez d’une plateforme à cet effet.
Obtenez une meilleure solution avec l’aide de SafetyCulture (anciennement iAuditor)le meilleur outil numérique que vous puissiez utiliser pour constituer avec précision les informations dont vous avez besoin pour analyser et identifier les déchets dans vos processus. Vous pouvez également utiliser SafetyCulture (iAuditor) pour :
- Annoter les documents ou apporter des modifications aux informations dans les boîtes de données qui seront modifiées pour que toute l’organisation puisse les voir en temps réel.
- Partager les informations de manière plus pratique grâce à la fonction “cloud”, accessible partout dans une application mobile.
- Contrôler les performances de votre équipe grâce à la fonction de suivi en temps réel et de suivi des indicateurs clés de performance.
- Effectuer la gestion des équipements grâce à des inspections numérisées pour vous assurer qu’ils fonctionneront sans problème pendant les opérations afin d’éviter les défauts et les temps d’arrêt.
- Vérifier la qualité de votre production et de vos produits finis à l’aide de la fiche de contrôle de la qualité pour vous assurer qu’ils répondent aux attentes des clients.