¿Qué es el proceso de validación?
La validación del proceso es un procedimiento paso a paso diseñado para garantizar que un proceso de fabricación pueda producir productos de calidad de forma constante. La realiza un equipo de validación dirigido por el responsable de la garantía de calidad de los fabricantes de la industria farmacéutica. Por lo general, la validación del proceso se realiza antes de lanzar un nuevo producto, al aplicar cualquier cambio en un producto existente y para verificar periódicamente el proceso. Establecido desde el principio, un protocolo debe especificar cómo se llevará a cabo el proceso de validación, incluidos los parámetros que se controlarán, las muestras que se tomarán y los resultados que se aceptarán.
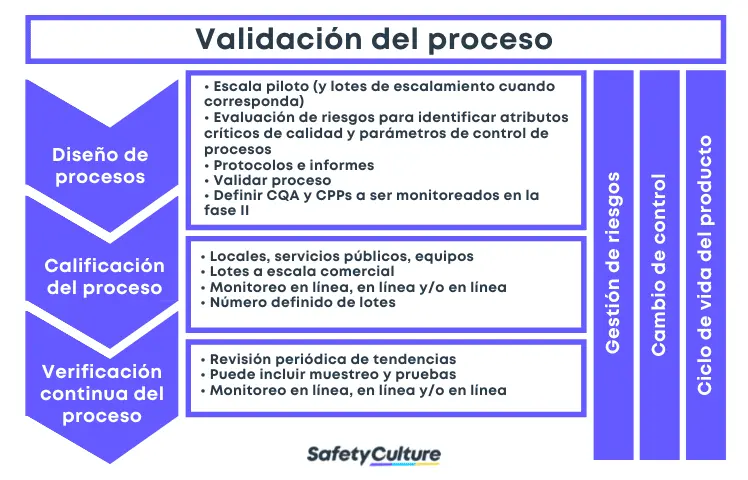
Fases de la validación de procesos | Fuente de la imagen
Guía de proceso de validación: FDA vs GHTF
La Administración de Alimentos y Medicamentos de los Estados Unidos ( USFDA) ) se discuten los principios y prácticas generales que los fabricantes pueden utilizar para validar los procesos de fabricación. Abarca diferentes categorías de medicamentos, como productos humanos, veterinarios y biológicos o biotecnológicos.
Una organización voluntaria de funcionarios de agencias reguladoras llamada Grupo de Trabajo de Armonización Global ( GHTF ) proporcionó directrices de validación de procesos para productos sanitarios. Su objetivo es ayudar a los fabricantes a comprender los requisitos relativos a los procesos de fabricación, mantenimiento e instalación de productos sanitarios. Finalmente, el Foro Internacional de Reguladores de Dispositivos Médicos ( IMDRF ) sustituyó al GHTF, asumiendo su misión de estandarizar la normativa sobre productos sanitarios en todo el mundo.
3 etapas de la validación de procesos
La USFDA hace hincapié en la recogida y evaluación de datos en su definición de validación de procesos. Es crucial que el equipo de validación no sólo reúna información sobre las actividades a lo largo del ciclo de vida del producto y del proceso, sino que también las analice para comprender los orígenes de la variación y controlarla en consecuencia. Las tres etapas de la validación del proceso son el diseño del proceso, la cualificación del proceso y la verificación continua del proceso:
Etapa 1: Diseño del proceso
Durante esta etapa de validación, el proceso de fabricación se define de manera que pueda reproducir la entrega de un medicamento que cumpla con especificaciones y atributos de calidad predeterminados. Para lograrlo, el equipo de validación debe tener una idea clara de cómo funciona realmente el proceso. Considere las siguientes fuentes y métodos para capturar la información del proceso:
- Actividades de desarrollo de productos
- Funcionalidad y limitaciones de los equipos de producción
- Contribuciones previstas a la variabilidad
- Estudios de diseño de experimentos (DOE)
- Herramientas de análisis de riesgos
- Experimentos o demostraciones a escala de laboratorio o piloto
- Simulaciones informáticas o virtuales
Esta etapa de validación también implica el control del proceso, planificando estrategias para reducir la variación de los insumos y/o ajustarse a ella durante la fabricación. Los controles suelen consistir en el análisis de los materiales y la supervisión de los equipos en puntos de procesamiento significativos. En algunos casos, el uso de la tecnología analítica de procesos ( PAT ) puede ser necesario.
Etapa 2: Calificación del proceso
La etapa de cualificación del proceso de validación del proceso implica la evaluación del diseño del proceso para determinar si es eficaz para la producción de calidad. En primer lugar, las instalaciones de fabricación deben diseñarse de acuerdo con los requisitos de las buenas prácticas de fabricación actuales (CGMP). Siguiente, calificación de los servicios y equipos debe llevarse a cabo, por ejemplo, asegurándose de que se construyen e instalados de acuerdo con las especificaciones de diseño . Finalmente, la calificación del rendimiento del proceso debe ejecutarse mediante un protocolo y documentarse en un informe:
- Introducción, objetivos y ámbito de aplicación
- Producción, Garantía de calidad (QA) y Control de calidad (QC) Responsabilidades y requisitos previos (por ejemplo, registros de fabricación)
- Plan de estudio de validación de procesos basado en la gestión de riesgos de calidad (QRM)
- Equipo de validación (investigación y desarrollo, ingeniería, producción, control de calidad y control de calidad)
- Detalles del producto y consideraciones de diseño
- Lista de materiales, proveedores y fórmula magistral
- Lista de equipos y diagrama de flujo del proceso
- Breve proceso de fabricación y evaluación de los parámetros críticos del proceso (CPP)
- Pruebas y especificaciones en proceso o atributos críticos de calidad (CQA)
- Muestreo, plan de pruebas y criterios de aceptación y límite
- Detalles del rendimiento (un mínimo de tres lotes consecutivos)
- Validación de métodos analíticos
- Especificación del producto acabado
- Revisión de las especificaciones no válidas ( OOS ) Resultados de pruebas, desviaciones y control de cambios (CC)
- Criterios de revalidación
- Revisión de las acciones de seguimiento (si las hay)
- Resumen y conclusión
Etapa 3: Verificación continua del proceso
Tras el diseño del proceso y la cualificación del mismo, la tercera etapa de la validación del proceso se ocupa de establecer sistemas que garanticen continuamente que el proceso validado se mantiene en ese estado durante la producción rutinaria. La verificación continua del proceso suele incorporar el uso del control estadístico del proceso (CEP), la supervisión y el muestreo continuos de los parámetros del proceso y los atributos de calidad, y el mantenimiento programado de las instalaciones, los servicios y los equipos. Es esencial para buenas prácticas de documentación que deben emplearse a lo largo del proceso de validación.
Cree su propia lista de verificación de validación de procesos
Elimine las tareas manuales y optimice sus operaciones.
Comience gratis4 tipos de validación de procesos
La validación del proceso se suele clasificar en función del momento en que se realiza en relación con el programa de producción. Sobre la base de esta descripción, existen 4 tipos de validación de procesos: validación prospectiva, validación retrospectiva, validación concurrente y revalidación.
Tipo 1: Validación prospectiva
Se aplica cuando cualquier producto se va a fabricar con una nueva fórmula o en una nueva instalación. También conocida como validación previa a la comercialización, la validación prospectiva suele llevarse a cabo antes de iniciar la producción rutinaria. También se considera el tipo de validación fundacional porque es el punto de partida de cualquier producto que vaya a salir al mercado en nuevas condiciones.
Tipo 2: Validación retrospectiva
La validación retrospectiva se lleva a cabo sólo cuando el proceso de fabricación no se ha sometido formalmente a una validación documentada. La validación retrospectiva se realiza normalmente con el uso de datos históricos y análisis de tendencias para proporcionar pruebas de que el proceso se encuentra en el estado que se pretende. En la mayoría de los casos, ya no es un enfoque aceptable para la validación del proceso porque cualquier producto debería haber sido validado antes de su distribución comercial.
Tipo 3: Validación Concurrente
Se realiza durante la producción farmacéutica regular para demostrar que el proceso funciona al nivel que debería en el curso de su ejecución real. Aunque la validación concurrente sigue siendo un enfoque aceptable para la validación de procesos en determinadas circunstancias (por ejemplo, la fabricación de medicamentos médicamente necesarios en coordinación con la USFDA para evitar una escasez de suministro), la agencia sigue haciendo hincapié en que sólo debe utilizarse en raras ocasiones.
Recientemente, una inspección de la FDA reveló que un fabricante con sede en EE.UU. producía productos farmacéuticos adulterados. Para corregir sus infracciones, la empresa farmacéutica respondió con la intención de aplicar la validación concurrente. Sin embargo, la USFDA advirtió en contra porque no mostraron una clara comprensión de las fuentes de variabilidad en sus procesos de fabricación. En cambio, la agencia les exigió que cumplieran con las normas específicas de las CGMP, incluida la validación adecuada de los procesos de fabricación.
Tipo 4: Revalidación
La revalidación está más extendida para los productos sanitarios que para los medicamentos. Se ejecuta cuando la validación prospectiva llega a la conclusión de que el proceso de fabricación es incapaz de producir el producto de forma consistente. Además, en el protocolo de validación original puede indicarse un criterio de revalidación. El proceso de revalidación puede no ser tan exhaustivo como la validación inicial, sobre todo si la situación sólo exige que se repitan algunos aspectos.
Ejemplos de validación de procesos
Un proceso validado no sólo disminuye la probabilidad de que se produzcan fallos en los lotes, sino que también aumenta la productividad de las instalaciones de fabricación, ya que se minimizan las repeticiones y los rechazos. Algunos ejemplos de procesos que deben validarse son la esterilización, el llenado aséptico, el tratamiento térmico, el chapado y el moldeo por inyección de plástico. En este ejemplo de validación de procesos farmacéuticos, un plan maestro de validación típico para procesos biotecnológicos contiene:
- Aprobación del Plan Maestro de Validación
- Mantenimiento del Plan Maestro de Validación (revisiones del documento e historial de revisiones)
- Definiciones
- Acrónimos
- Objetivo del Plan Director de Validación
- Alcance del Plan Maestro de Validación
- Estrategia de validación del proceso (introducción, calificación del soporte, parámetros críticos del proceso, número de ejecuciones a realizar y Resultados no conformes )
- Documentación de validación de procesos (Protocolos, informes, documentos estratégicos/evaluaciones y conservación de registros)
- Funciones y responsabilidades (servicios técnicos, operaciones, ingeniería, laboratorio de control de calidad, garantía de calidad y servicios externos)
- Descripción del proceso
- Descripción de la validación del proceso (documento y apoyo a la cualificación de las estrategias de retención y mezcla)
- Mantenimiento del estado validado y calificado (Programa, Mantenimiento preventivo y Calibración Revisión anual del producto, control de cambios, revisión periódica y verificación continua del proceso)
Establecimiento de pruebas documentadas de procesos controlados
La documentación es un elemento clave para el éxito de la validación del proceso. SafetyCulture (antes iAuditor) es una herramienta de recogida y evaluación de datos diseñada para facilitar a los equipos de validación la documentación de la información relacionada con el proceso, la ejecución del protocolo de validación y la actualización de todos los registros. Con SafetyCulture (iAuditor) los fabricantes pueden aportar pruebas de su capacidad para controlar los procesos de fabricación de productos farmacéuticos:
- Utilice plantillas de informes de validación de procesos en dispositivos móviles como smartphones, tabletas y iPads, incluso sin conexión.
- Capture las pruebas fotográficas de las diferentes etapas de la validación del proceso y anote las imágenes para mejorar la referencia visual.
- Cree al instante informes de validación compartibles y de aspecto profesional con todos los archivos adjuntos necesarios con sólo un toque de dedo.
- Archiva automáticamente los documentos en un almacenamiento seguro en línea que también puede descargarse como PDF y enviarse al personal designado por correo electrónico.
- Añade hasta 10 empleados o miembros del equipo de validación utilizando una cuenta gratuita de SafetyCulture (iAuditor) .