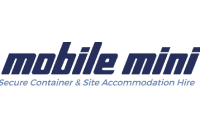
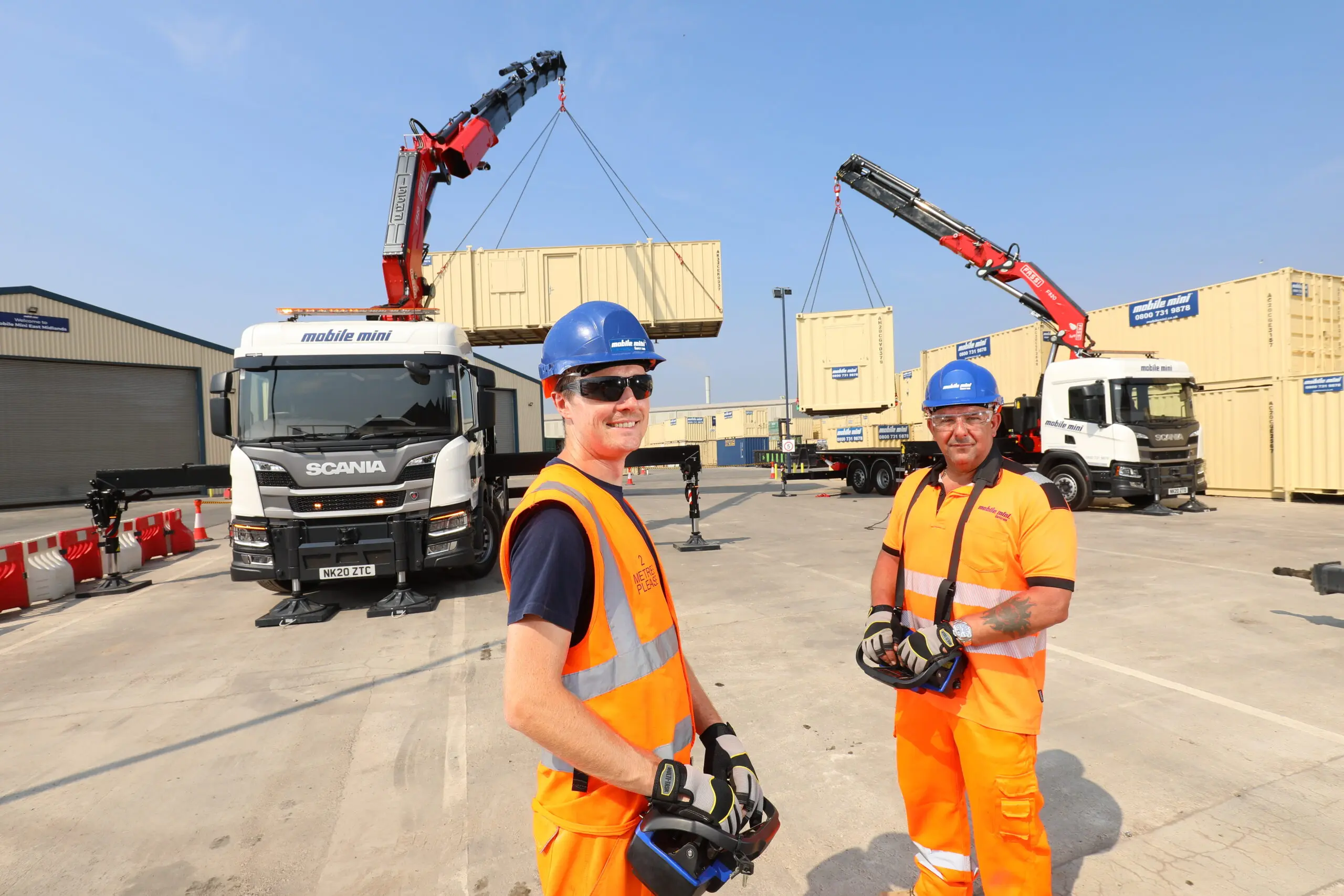
Mobile mini
Returning every employee home safe is at the heart of Mobile Mini’s ethos. Follow their journey to a safer workplace.
Quality isn’t just about the product. It’s the systems, procedures, and people involved in the process.
75 Years in Manufacturing Business
220,000 Square-Foot Manufacturing Facility
700+ Audits Completed In 18 Months
Craig Lennie’s career progression is diverse, to say the least. Before coming on board as the Quality Assurance Manager for Gason, he ran his own business in the retail sector and was even an Officer in the Royal Air Force. Through all these different roles he’s learned one important thing: quality must always come first.
That’s why when he joined Gason in November 2017 he immediately began identifying opportunities for improvement. As one of Australia’s leading Design, Manufacturing and Engineering Companies, Gason products are already renowned for quality – its motto is ‘built to last’. Founded in 1946, not every element within Gason’s 220,000 square-foot manufacturing facility in Victoria, Australia managed to keep pace with the fast wave of technology disruption taking over the manufacturing industry.
Quality isn’t just about the product,” Craig explains. “It’s the systems, procedures, and people involved in the process.
Initially, Craig’s goal was to minimize the team’s time spent auditing, and ensure critical stakeholders could access important information without adding to a pile of paperwork.
“The information I needed often wasn’t available, I wasn’t being correctly informed, and there was a lack of cold, hard data,” says Craig. “I was concerned because there was often quite a bit of guesswork, and stories would change.”
Craig needed to reduce the risk of any compromise to Gason’s reputation for excellence and began searching for a system to ensure no small error would be overlooked. When one of his co-workers came across SafetyCulture (formerly iAuditor), Craig decided to give it a try. “I remembered a Gason customer had previously recommended the software, and I could see its potential to add value to the business – and really springboard us into the 21st century,” says Craig.
However, since Gason is a huge company with four distinct business streams, Craig needed to start small. “When you’re introducing new software into a long-established business, it’s often difficult to effect immediate change company-wide,” he explains. So Craig tested the waters by implementing SafetyCulture platform into his own team’s internal auditing processes before slowly introducing it to other business centers within the company.
“We’re now using SafetyCulture platform to conduct quality checks in three of our four business streams,” says Craig.
I remembered a Gason customer had previously recommended the software, and I could see its potential to add value to the business – and really springboard us into the 21st century
Since implementation, Craig has continued to be pleasantly surprised by the unique possibilities of SafetyCulture platform. “One of my favorite things about the software is that we can adapt it for specific purposes. As it’s easily customizable, we have the flexibility to integrate it seamlessly within our existing processes,” says Craig.
He was also impressed by how quickly Gason’s factory floor workers familiarized themselves with the new mobile technology. “They’re happy because we’ve removed needless paperwork from their workspace,” Craig explains. “Now, they can just use a phone or iPad to sign off, report and make comments – which is such an improvement since those guys are often covered in oil and grease!”
Other benefits include:
“SafetyCulture platform has improved our processes and helped us identify elements in the business that need to be eradicated or updated – we’ve saved huge amounts of time.”
“Not only has it facilitated better internal communication, it’s made collaboration with our suppliers and customers a first-class experience. One of our customers is even using SafetyCulture platform, so we can liaise with them in real-time. That means we’re confident every element, from pre-production checks and freight to measurements and auditing, is as streamlined as possible.”
“My goal was to shift the culture of quality beyond product – and we’ve been successful. These days, we’re not just conducting quality checks when a machine or item is walking out the door, we’ve inspired every employee to take ownership of the quality of their workmanship.”
But of course, for Craig, the most important benefit is the certainty he now carries with him into work each day. “All I have to do is check my SafetyCulture platform dashboard in the morning, and update my inventory report software. I have complete visibility – which helps me ensure the future is healthy,” he says.
“Anything that is built by Gason is built to last. We expect it to serve its purpose and have longevity. We’ve been here 75 years, and we want to be here for another 75 years.”
Now, they can just use a phone or iPad to sign off, report and make comments – which is such an improvement since those guys are often covered in oil and grease!
Anything that is built by Gason is built to last. We expect it to serve its purpose and have longevity. We’ve been here 75 years, and we want to be here for another 75 years.
Returning every employee home safe is at the heart of Mobile Mini’s ethos. Follow their journey to a safer workplace.
Creating an improvement culture by tapping into the power of data
How Schneider Electric cut auditing time and broke down information silos.
Explore more stories, expert guides, and thought leadership from SafetyCulture