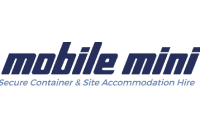
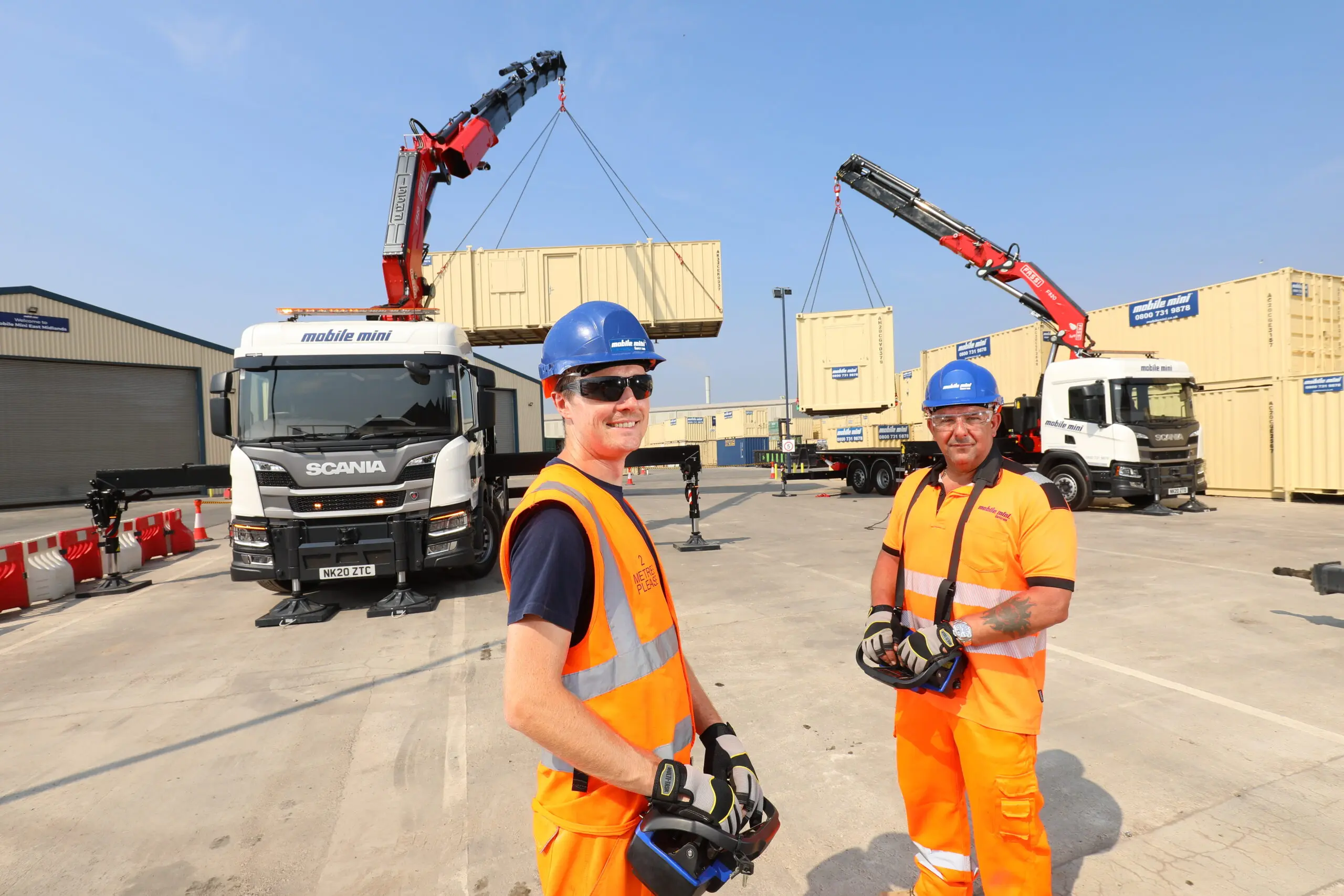
Mobile mini
Returning every employee home safe is at the heart of Mobile Mini’s ethos. Follow their journey to a safer workplace.
Aerial construction and maintenance can be a high-stakes game. Learn how Infravision uses SafetyCulture (formerly iAuditor) both on and off the ground.
From 5-10 minutes to flag problems to a 30-second process in the SafetyCulture platform
Aerial construction and maintenance can be a high-stakes game. Power lines are a legacy risk for workers in the energy and utilities industry. But Infravision saw another way forward — using autonomous technology to deliver safer, cheaper, faster, and greener solutions, all without putting any lives on the line.
Working at heights operations are baked into traditional industry practices. As an Australian Civil Aviation Safety Authority certified company, Infravision utilizes TX systems and drones to minimize high risks tasks for construction workers.
But it’s not just the aerial technology at work here. It’s also the tools and the systems that are working behind them to create a much safer environment and add valuable information. SafetyCulture platform is their team’s companion both on and off the ground. Here’s how they get it done.
Infravision’s employees partner with construction workers on the frontline, working on energy easements not just around Australia, but all around the world. It’s an enormous operation to track and one that was initially taking place on a paper-based system, that would then be translated into Excel.
This meant lots of doubling back and dispersed data, when really what Infravision required was timeliness and visibility. The nature of the work had Infravision’s teams out in remote regions carrying out high-risk activities, whether it was constructing or carrying out maintenance activities on transmission and distribution networks. When SafetyCulture entered the picture, Infravision quickly implemented the platform end to end across their whole project life cycle. This meant that everything — from the very first onsite reconnaissance to drone preflight checks and customer feedback — was all housed in a single platform.
The Issues feature in particular became a real gamechanger. It enabled workers to flag any incidents, hazards, workplace, incidents, or injuries as they occurred.
“We’re able to ensure that we have a real direct link with our frontline workers and our customers, and it’s a two-way street. It’s about empowering our frontline workers to be able to notify us of anything that’s happening out there in the field or in the factory.”
More than just notifying the right people, Infravision has a company policy that mandates action be taken to help resolve Issues, triggering a workflow that closes the loop.
“The reality is that mediums like a text or a phone call, while they’re great to get an initial notification, they don’t provide a tracking capability and historical records can be lost,” shares Paul.
The reality is that the lack of timeliness is one of the real challenges when it comes to issues reporting in the workplace. Teams are busy so when something happens, more often than not, the day moves on and those issues and incidents can be lost over time. With Issues, Infravision found a really easy way for frontline workers to interact and raise issues as they happen.
And these Issues don’t necessarily have to be related to incidents or injuries either. Infravision uses the feature to capture customer feedback, creating categories that allowed customers to scan QR codes and log feedback directly. This direct input into safety management and quality systems helps to create a continuous improvement feedback loop that Infravision can harness to get better every day.
“Safety is absolutely the forefront of everything we do. One of the terms that we use at Infravision is ‘high-reliability organization’, driven by the fact we can be better tomorrow than we are today. We have to be learning every day and what’s critical in developing that sort of culture is the ability to report on it, to empower our workers and our customers to provide us that feedback and to track how we’re improving the workplace and our product.”
One of the foundational pieces of becoming triple ISO certified is demonstrating a quality management system and a safety management system. SafetyCulture platform helped Infravision to cover off the end-to-end processes needed to prove compliance. Organizations must recertify for ISO compliance every 3 years. But best practice is to perform internal continuous assessments throughout the certification period. Thorough annual self-assessments and smaller, more frequent checks are also encouraged. By baking SafetyCulture platform into their everyday procedures, Infravision was one step ahead of the process.
“It’s really been one of the foundational pieces of us being successful in getting our ISO certification, which is really critical for us as a business.
Returning every employee home safe is at the heart of Mobile Mini’s ethos. Follow their journey to a safer workplace.
The largest solar panel installation contractor uses SafetyCulture (formerly iAuditor) to train employees and track safety in the field.
This construction firm saves 1,500 man hours per year with SafetyCulture (formerly iAuditor).
Explore more stories, expert guides, and thought leadership from SafetyCulture