What is Arc Flash?
Creating an Electrically Safe Working Condition (ESWC) is possible but it may still require workers to interact with energized equipment. The possibility of an arc flash occurring in an ESWC is one of the most severe problems in the electrical industry.
An arc flash, also called a flashover, is a sudden electrical explosion or discharge that happens when electric current travels through the air from one conductor to another. According to Electrical Safety U.K., an arc flash can reach 20,000°C, which is four times the heat of the sun. The resulting sound is similar to a firecracker popping or a gunshot. Examples of arc flash occurrences include lightning and the use of an electrical arc welding machine.
This phenomenon may happen at a small scale such as whenever equipment is being installed or removed, or when disconnecting switches. It can be damaging in a split second, producing fires or major injury to workers who come into close contact with it. When an arc flash occurs, the results can be extremely violent, and if a person is in close proximity to the flash, they can suffer injury or even death.
Causes
An arc flash can be caused by an electrical fault in a power distribution system. Faulty wiring, loose connections, failure in the electrical system of a building or structure, or even faulty equipment can also cause an arc flash. It may occur in small spaces, such as a crawl space under a house. It can also occur in large spaces, such as a basement, or in a machine room.
Workplace Safety Awareness Council has given examples of its causes in their handouts on arc flashes. They are the following:
- Dust
- Dropping tools
- Accidental touching (of two conductors)
- Condensation
- Material failure
- Corrosion
- Faulty installation
Danger
- When it pertains to the severity of an arc flash injury, three factors come into play:
- Proximity of the worker to the event
- Size of the explosion
- Time exposed to the hazard
Typical injuries and results from an arc flash include:
- External and internal burns
- Intoxication from the inhalation of hot gases or of vaporized metal
- Eye damage and blindness caused by the ultraviolet light of the arc flash
- Fire that could spread rapidly through a building
- Flying molten metal
- Extremely high pressure
- Ear damage caused by a sound blast
- Heat (upwards of 35,000°F or 20,000°C)
It is also possible that an explosive force (known as an arc blast) will be formed, depending on the severity of the arc flash.
Arc Flash Hazard Management
Although the possibility of an electric arc forming is low, the severity of the resulting damage can be severe. Control measures can be implemented to minimize the risk of an arc flash occurring in the workplace. The National Fire Protection Association (NFPA) details how to comply with the Occupational Safety and Health Administration (OSHA) regulation through the NFPA 70E standard.
NFPA 70E: Standard for Electrical Safety in the Workplace® (2015 edition) addresses electrical safety and contains the requirements to perform shock and arc flash hazard management.
NFPA 70E is a national consensus safety standard that identifies safe work practices to ensure workers’ safety from electrical hazards. According to NFPA 70E, only trained and qualified employees are permitted to work on or near exposed energized electrical parts, and they must supervise unqualified personnel who are in the proximity of the hazard. NFPA 70E states “This standard addresses safety of workers whose job responsibilities entail interaction with electrical equipment and systems with potential exposure to energized electrical equipment and circuit parts.”
Create Your Own Arc Flash Checklist
Eliminate manual tasks and streamline your operations.
Get started for FREELimits of Approach by NFPA
NFPA 70E has developed specific approach boundaries designed to protect employees while working on or near energized equipment. In the Informative Annex C of NFPA 70E (2015 edition), an illustration was given on the limits of approach, which are boundaries for protection in working. Below is an infographic showing the limits of approach:
- Arc Flash Protection Boundary (outer boundary)—this is the farthest boundary from the energized equipment. If an arc flash occurred, this boundary is where a worker could receive a curable, first-degree burn. Workers must not cross this boundary unless they are wearing proper electrical Personal Protective Equipment (PPE).
- Limited Approach—this is the distance where barriers should be placed to protect personnel. An approach limit is set at a distance from an exposed live part in the presence of a shock hazard.
- Restricted Approach—this is the distance wherein there is an increased risk of shock. Only qualified personnel are allowed and with the appropriate PPE based on the required protection.
- Prohibited Approach (inner boundary)—this is a distance from an exposed component that is the same as the distance between the exposed component and the live part. However, the “prohibited approach” boundary was removed in the 2015 NFPA 70E edition.
The limit of approach varies among equipment. Some equipment will have a bigger flash protection boundary while others will have a shorter flash protection barrier.
4 P’s Model
Another effective way to help prevent arc flashes is to use the 4P Model for arc flash hazard management: Predict, Prevent, Protect, Publish.
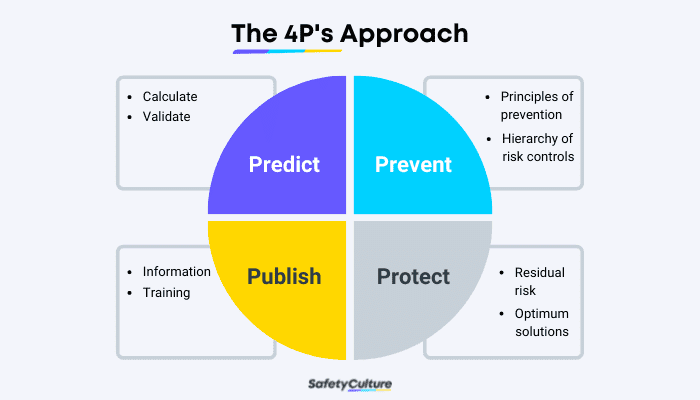
The 4P’s Approach
- Predict—pertains to identifying and calculating the potential risks by making an arc flash study. It is advised that the Institute of Electrical and Electronics Engineers (IEEE) 1584 Guide for Performing Arc Flash Hazard Calculations 2002 be utilized when predicting the severity of the effect of an arc flash.
- Prevent—pertains to mitigating the use of principles of prevention or the hierarchy of controls in designing, planning, or eliminating the risk.
- Protect—pertains to reducing the risk of injury with proper protection or PPE if the hazard can’t be removed.
- Publish—pertains to collecting information for risk assessment and use in training, as well as providing safety warning labels where the risk cannot be eliminated.
Arc Flash Warning Labels
In compliance with NFPA 70E, energized equipment should be installed with warning labels, such as arc flash stickers (also known as electrical hazard labels). These warning labels inform workers about the potential of electrical explosion or high voltages.
The 2017 edition of NFPA 70®: National Electrical Code states in Article 110.16: “Electrical system, such as switchboards, switchgear, panelboards, industrial control panels, meter socket enclosures, and motor control centers that is in other than dwelling, and is likely to require examination, adjustment, servicing, or maintenance while energized, shall be field or factory marked to warn qualified persons of potential electric arc flash hazards…The marking shall be located so as to be clearly visible to qualified persons before examination, adjustment, servicing, or maintenance of the equipment.”
It also states that labels shall contain the following:
- Nominal system voltage
- Fault current at the service overcurrent device
- The clearing time of service overcurrent protective devices based on the available fault current at the service equipment
- The date the label was installed
Modifications are made to the labeling in the NFPA 70E. In order to properly protect workers from arc flashes, you will need to provide the following information:
Parts of the Labels
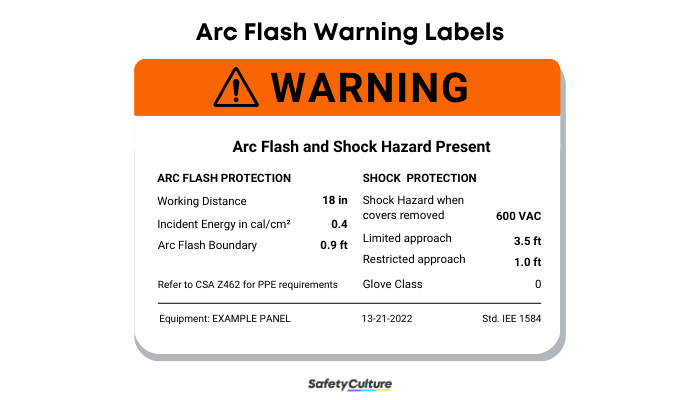
Arc Flash Warning Labels
- Danger or warning header
- Working distance—the distance of the worker from the arc source
- Incident energy—the thermal energy amount
- Arc flash boundary—the distance where someone standing in the boundary might get a second-degree burn if they are not wearing protective clothing
- “Shock Hazard When Cover is Removed”—the voltage level of the equipment
- Limited approach boundary
- Restricted approach boundary
- Glove class—the proper rubber insulated gloves
- Arc flash PPE category requirement
Personal Safety and Protective Equipment
In the revised version of NFPA 70E published in 2018, one of the major changes was including the hierarchy of controls in its standard regulations. Specifically, the standard now states that the elimination of the hazard must be the first and foremost priority. Performing energized work with PPE as a last line of defense is also heavily emphasized in the latest update on NFPA 70E.
Arc Flash PPE Categories from NFPA 70E (2015)
NFPA 70E (2015) classified personal protective equipment into four categories, with each category containing the minimum Arc Rating value for the PPE that is required.
Category 1: Minimum Arc Rating of 4 cal/cm2 | Category 2: Minimum Arc Rating of 8 cal/cm2 | Category 3: Minimum Arc Rating of 25 cal/cm2 | Category 4: Minimum Arc Rating of 40 cal/cm2 | |
Arc Rated Required Clothing | AR Long Sleeve Shirt and Pants or AR Coverall | AR Long Sleeve Shirt and Pants or AR Coverall | AR Flash Suit Jacket andPants or AR Coverall | AR Flash Suit Jacket and Pants or AR Coverall |
Required AR Face and Head Protection | Face Shield or Arc Flash Suit Hood | AR Flash Suit Hood or AR Face Shield and Balaclava with minimum arc rating of 8 cal/cm2 | AR Flash Suit Hood | AR Flash Suit Hood |
Required AR Hand Protection | N/A | N/A | Rubber insulating gloves and leather protectors or AR gloves | Rubber insulating gloves and leather protectors or AR gloves |
As Needed | AR Jacket, Rainwear, Parka, Hard Hat Liner | AR Jacket, Rainwear, Parka, Hard Hat Liner | AR Jacket, Rainwear, Parka, Hard Hat Liner | AR Jacket, Rainwear, Parka, Hard Hat Liner |
SafetyCulture (formerly iAuditor) for Electrical Safety
Arc flashes and electric shocks can result in fatal injuries. Ensuring that you have the right controls in place to minimize the possibility of an arc flash is essential for the safety of your workers and the proper operation of your company. To avoid these dangers, careful management, attention to detail, and technical expertise are required—all of which can be streamlined using SafetyCulture.
- Manage electrical safety by using SafetyCulture, one of the best platforms to conduct risk assessments and inspections to identify potential electrical hazards in your workplace. You can also use the platform to:
- Conduct digitized inspections by using Digital Electrical Inspection Checklists.
- Conduct accurate audits to check if PPE is available to workers and if the equipment is properly labeled.
- Monitor your operations through more efficient reporting by using the Accident Report Form Checklist and other helpful checklists such as Electrical Hazard Checklist before commencing electrical tasks.
- Train staff on proper safety procedures and lockout-tagout practices
- Manage assets and ensure they are safe for use in different situations and environments
- Assess the compliance of electrical safety measures in your workplace such as switches, power lines, appliances, installations, wiring, cables, and cords by using the Electrical Safety Inspection Report Checklist.