What is GLP?
Good Laboratory Practice (GLP) is a quality system covering the organizational process and conditions under which non-clinical laboratory studies are planned, performed, monitored, recorded, reported, and archived. GLP ensures the quality and integrity of safety test data submitted to the government for the issuance of research permits.
GMP vs GLP
The difference between GMP and GLP is their scope. Good Manufacturing Practice applies to the entire drug manufacturing process while Good Laboratory Practice applies only to the safety testing phase. Both GMP and GLP are enforced by the Food and Drug Administration (FDA) in the United States.
Do You Need to Comply with GLP?
Below is a table based on FDA guidance to help research laboratories determine if a specific study or activity must comply with Good Laboratory Practice:
GLP Compliance Required |
GLP Compliance Not Required |
|
|
GLP is also not required during early development stages such as discovery, screening, basic research, and concept assessment. According to the World Health Organization, GLP compliance is typically limited to Stage 2 of the drug development process.
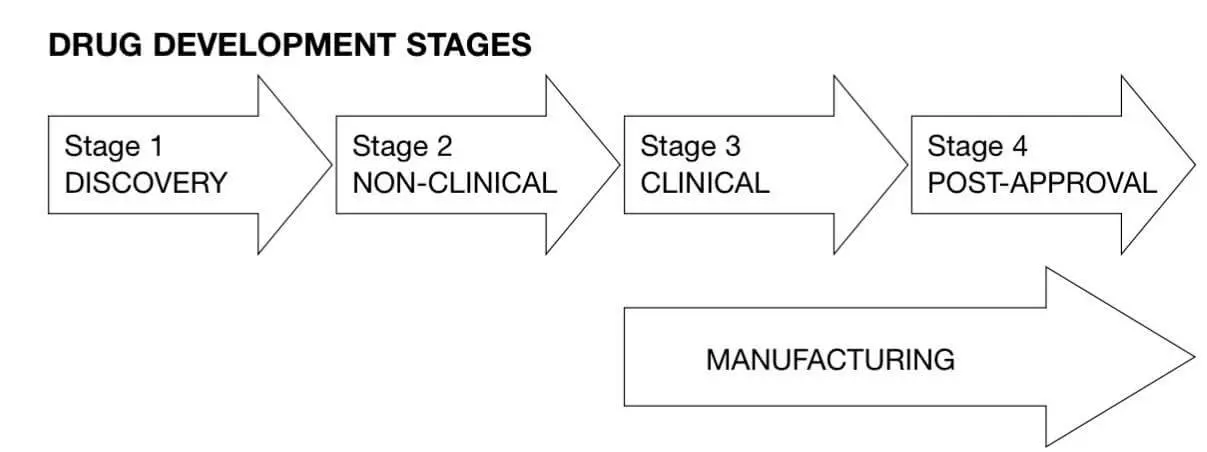
Image source: WHO TDR GLP
Definition of GLP Terms
Testing facility or test facility – the research laboratory conducting the non-clinical study
Test article or test item – the product being studied or tested; the subject of the study
Test system – these are:
- any animal, plant, microorganism to which either the test or control article is applied
- any biological, chemical, or physical system used in the study
Control article or reference item – a product that is:
- not the test article, feed, or water
- applied to the test system
- used to provide a basis for comparison with the test article
Good Laboratory Practice Guidelines
Below are Good Laboratory Practice guidelines for the different elements of a study:
Personnel
Before the study begins, the testing facility manager must appoint a study director who will be responsible for the overall conduct of the study and its GLP compliance. The testing facility must also have a Quality Assurance Unit (QAU) which is separate from or independent of the testing facility organization or management.
Facility & Equipment
The testing facility should provide separation of activities to prevent interference and other disturbances which may compromise the study. There must be separate areas for:
- the receipt and storage of the test and control articles
- the mixing of the test and control articles with a carrier
- the storage of the test and control article mixtures
- the housing of the test systems
All equipment used in the study should be periodically calibrated and maintained. Records of calibration and maintenance should be kept and made available to operators of equipment
Characterization
Personnel performing the study should know the following about each test and control article:
- identity, purity, composition, and stability
- date of receipt, expiry date, and storage instructions
- quantity received and quantity used
Study Plan or Protocol
The study plan or protocol is the master guidance document for the conduct of the study. It outlines how the study should be performed and contains the general time schedule for the study and its various stages. It also includes the method and materials used in the study.
The protocol must go through approval, review, and discussion before the study begins. This process starts with the study director preparing the protocol and discussing its contents with personnel and other study staff. After discussion, the study director must then approve the protocol by affixing their dated signature.
Once the protocol has been approved by the study director, it must be reviewed by the QAU, who will assess its compliance with Good Laboratory Practice. At this point in the process, personnel should be instructed on the duties assigned to them in the protocol as well as receive their own copies of the protocol.
Standard Operating Procedures
Each of the separate areas in the testing facility should have Standard Operating Procedures (SOPs), especially for routine procedures. SOPs must be approved by the testing facility manager and any deviations from SOPs need to be authorized by the study director.
Final Report
The final report is ultimately the responsibility of the study director, who prepares and approves the report. Key features of the final report are:
- a complete and accurate account of the conduct of the study
- any deviation from an intended course of action (such as SOP or protocol)
- scientific interpretation of results and critical discussion
- GLP Compliance Statement by the study director
Storage of Records
Throughout the course of the study, the study director will be responsible for ensuring that all data pertaining to the study is captured and included in records that are safely stored. These records and documents such as the protocol, the final report, and standard operating procedures will then be archived at the end of the study.
Only personnel authorized by the testing facility manager can access archived records. Additionally, every instance of records being accessed, removed from, or returned to the archives must be logged. It is also recommended that records in the archives be indexed for organized retrieval.
Retention of Records
The required retention period for archived records varies depending on national GLP regulations. For research laboratories in the US, use the following guide questions based on Subpart J of 21 CFR Part 58 (“Good Laboratory Practice for Nonclinical Laboratory Studies”):
- Were the results of the study submitted to the FDA?
- If YES: Is the study supporting an Investigational New Drug (IND) application or an application for Investigational Device Exemption (IDE)?
- If Yes: Archived records must be retained at least 5 years after the date on which the results of the study were submitted to the FDA.
- If No: Archived records must be retained at least 2 years after the date on which the application for a research or marketing permit was approved by the FDA.
- If NO: Archived records must be retained at least 2 years after the date on which the study was completed, terminated, or discontinued.
- If YES: Is the study supporting an Investigational New Drug (IND) application or an application for Investigational Device Exemption (IDE)?
Create Your Own Good Laboratory Practice Protocol Template
Eliminate manual tasks and streamline your operations.
Get started for FREEGood Laboratory Practice Examples
Below are general Good Laboratory Practice examples:
- Wear Personal Protective Equipment (PPE) at all times.
- Communicate with other members of the research lab.
- Participate in refresher training and safety exercises.
- Be aware of what you’re doing at all times.
- Pay attention to unfamiliar smells and substances.
- Use the right lab equipment for the task or activity.
- Regularly clean, calibrate, and maintain equipment.
GLP Requirements
GLP regulations in the US, UK, and EU have similar GLP requirements since they are members of the Organization for Economic Co-operation and Development (OECD). This international organization developed the GLP principles used in many countries today.
The 10 Good Laboratory Practice principles are:
- Test Facility Organization and Personnel
- Quality Assurance Programme
- Facilities
- Apparatus, Material, Reagents
- Test Systems
- Test and Reference Items
- Standard Operating Procedures
- Performance of the Study
- Reporting of Study Results
- Storage and Retention of Records and Materials
How GLP Training Can Help You Implement Workplace Best Practices
Building a culture of quality and safety in the workplace goes beyond just having a set of how-to guidelines. It’s about fostering the right mindset among your workers so that safety becomes second nature to them. One way to do so is through GLP training.
Transforming your how-to guides into interactive training can help educate your workers on the safe and proper procedures observed in your workplace. It’ll help increase their awareness and understanding of potential hazards they face at work, allowing you to build a consistent approach to safety throughout your organization.
Forget about dull and boring training. With SafetyCulture (formerly iAuditor)’s Training feature, you can transform your how-to-guides into visually stunning slides that’ll captivate and engage your team from start to finish.
You can also make training courses accessible to your team using their preferred devices. With Training’s offline access, they can brush up on GLP best practices even without an internet connection.
How SafetyCulture Can Help with GLP Regulations Compliance
SafetyCulture is a recognized quality management software that testing facility managers, study directors, and QA/QC professionals can use for GLP regulations compliance. SafetyCulture can be used at every step of the Good Laboratory Practice program, from preparing the study plan or protocol to submitting the final report for QA review.
SafetyCulture features for GLP regulations compliance:
- Customizable template editor: Make any kind of document or form with various template item types and smart logic. Record data conveniently on the mobile app.
- Easy yet comprehensive inspections: Conduct study-based, facility-based, and process-based inspections using any tablet or mobile device. Add photos, detailed notes, and assign corrective actions to laboratory personnel.
- Sleek, automated reporting: Simply complete an inspection to get a PDF and Web report of the inspection or audit. Immediately email reports to supervisors or save them for future reference.
- Engaging Training: Train workers in the proper implementation of GLP practices and compliance with GLP regulations.
- Asset Management: Ensure the safety and quality of equipment and other assets in the laboratory by registering, managing, and maintaining them using one platform.
Available as a web-based software and as a mobile app, SafetyCulture is free to download and has a free plan with all of the features mentioned above. Get started with SafetyCulture for free!